Our Kitchen: the Ups and the Downs of this Project

I have been pretty consistent with keeping you all in the loop about my kitchen progress on social media, but I actually haven’t really discussed the ups and downs at great length and I thought this would be the appropriate platform for to do so. I have many people exclaiming how my kitchen seems to be a bit of disaster with all of the issues I’ve been having, as well as that it’s been taking far too long to be completed, but to be honest this project is not unique. One thing that I’ve learned about the process of renovations, is that there are a lot of hiccups that happen along the way and it is impossible to control all of them. I mean there are just so many variables and not one project is the same, because not one home is the same! So you can never truly know going into a renovation exactly how it will go and what will come up as it’s happening.
One thing is for sure, I am grateful to have gone through this process on my own so now, I can truly empathize with my clients and be able to perhaps console them a little better when they’re dealing with their own renovations. One would think the interior designer would be immune to most project mishaps but amazingly, they’re not and perhaps the mishaps are either handled differently or made aware more frequently, than if it were a client where the interior designer figures out a lot of the issues and creates the resolutions without the clients being aware. As the client and the designer in this project I am aware of everything as it happens. Also since you, the audience have been learning about the issues in real time, perhaps are all little more enlightened to the how many issues can come up in one given project.
Which leads me to the purpose of this post. I thought I would perhaps discuss the biggest hiccups or speed bumps that we’ve experienced along the way and then provide some sort of guidance or realistic expectations to you as a client or a DIY renovator if you are to be in this situation in the future (or even currently). I think the easiest way to break it all down is to discuss the ‘issues’ based on the major design elements that go into every kitchen renovation; contractors and subcontractors (electrical, plumbing, etc), flooring, appliances, cabinets, hardware, paint and/or finishes, countertops, backsplashes, and lighting.
Contractors + Subcontractors
The very first major element to any renovation is selecting your contractor(s). This definitely includes your interior designer and or architect if needed. I could do a whole post on these contractors alone, but I don’t really have the time nor your attention to focus on that now. So perhaps you can keep the general contractor and subcontractor tips in mind as a general rule when selecting interior designers and architects as well.
In our own project we struggled with hiring a contractor quite honestly because Jack and I are both very handy, knowledgeable and experienced when it comes to house projects. My skills as an interior designer and his history as a lead carpenter and building houses with his dad, makes us both obvious candidates for a DIY kitchen renovation. However, the most important factor as to why we decided to leave this up to the professionals is our own availability of time. Jack now works full-time and makes a pretty good living doing it in tech. He would not by any means have the availability needed to complete this renovation in a timely manner. I also believe that part of it alone would put a huge strain on our relationship. I also do not have all the time in the world. My time may flexible, but I would have to take a huge cut in my workflow (and income) if I were to take on managing this project full time.
We ended up settling on a local contractor that typically handles small to mid-size commercial and residential renovations. They had plenty of experience in older home renovations and working with what can sometimes be considered ‘scrappy’ budgets for restaurant clients. We also selected this contractor not only because they were in our budget range, but also that they were extremely easy to communicate with and I felt comfortable being the main person in communication, speaking with them about my wants, needs and money. Because believe me, I have felt the weight of the patriarchy many times as woman leading projects and the last thing I wanted was to be seen as is ‘less than’ or disrespected in any way by my contractor. Lastly, they came well recommended and I happen to love several of the projects they’ve built and the people they have worked with!
Fortunately this relationship has been mainly positive and my initial thoughts or intuitions have reigned true (which they always seem to - props to me for listening to my gut). Our contractors are very communicative, respectful and kind people to work with. I do however still slightly wish that I could be less involved, because I have been spending a lot of time I didn’t plan on and have been doing a lot of management on my end for this project. I can’t say it’s my contractor’s fault, probably a lot of it has to do with me being the client, but I do wish I could step away a little more at times.
My greatest problem with the entire element of having a contractor which I’ve heard is very common is that I’m not in love with most of their subcontractors. The major bonus to hiring a contractor is that you are given the easy in on their specialty list of subs and typically that should make workflow and timelines run more smoothly. On the flip side to this, I’ve learned it does not mean you really know the subcontractors or their work ahead of time. You just kind of have to trust the portfolio of the general contractor and hope that their they are using the same subs for your project. You also have to hope that their reasons for using those subs are inline with your reasons or expectations. In the case of our project, I have not had the best experience with their electrician, nor have I been very happy about their plumber. And perhaps if I were to do this again I would probably have pushed back more on using our own subs in those circumstances. I have had good experiences however with the stone fabricator, flooring contractor and painters.
We ended up using a company to order our cabinets from that was different from our contractor’s recommendation. And that was only because the company they recommended would not/could not make inset style cabinets. We did not have the budget for completely custom, but needed semi-custom and in the end my design needs outweighed any other reasons in making this decision and we went with a different company. My contractor although not entirely happy with our decision, was respectful and agreed for us work with someone else.
So a few hiccups we’ve experienced on our project relating to the subcontractors are some errors by plumbers that made the propane company very unhappy with their portion of the install, as well as a major change order we had to pay for, because we forgot to include the potfiller in the final estimate (even though it was in the images we provided in the boards). Also, we’ve learned that because our contractors work on other larger projects that have bigger budgets than ours, we tend to be set lower on their priority list. This admittedly is a little frustrating at times. But understandable as a business owner - something you may want to consider when selecting your contractor however. So to get to the point.
Things to keep in mind when selecting your contractor:
Review their portfolio and check references - same goes for any subcontractor you hire individually, interior designer or architect.
Trust your gut on personality fit - this is so important and it’s hard to sometimes know because there’s not black and white factor in making a decision here. But if you don’t love the way your initial meetings go with the contractor, or if you have some red flags initially, bring them up and ask any questions you may have, because those flags will bite you in the butt if you don’t! Remember you will always look at the project with rose colored lenses before you start. If you hear something along the lines of them being down in staff or whatever, that is something that your subconscious took note of and you need to revisit, because again that may come up in the future to bite you in the butt.
Be extremely honest about your budget and tell the contractor that your budget is X, INCLUDING the taxes and contingency fees. Because if you don’t, they’ll use your budget as the baseline then add in the taxes, their markup and the contingency fees. Also, there will ALWAYS be change orders so be prepared for that! I would save about 10% of your budget for change orders and reduce the budget you’re providing to your contract with that 10% deducted.
Be very specific in reviewing your contract and make sure before you sign on that you have included EVERY SINGLE detail (that you can think of). This is something I somehow missed for a few elements and am kicking myself for! I.e. trim and mouldings for some reason did not mean ALL trim and mouldings. Crowns were not ‘listed’ so those would have to be change orders… and guess what we’re handling those ourselves now!
Be very clear about your needs as a client and their time commitment to your project on a weekly or monthly basis before signing the contract. It is also a good idea to get a history of their project turnover times and how often they plan to take vacation. This may sound silly, but I know too many people who have had contractors take multiple vacations during renovations that the clients were unaware of beginning the project. Everyone deserves a vacation, but as clients we also deserve to know when and how often vacations happen.
Our floors - new next to old
Flooring
Depending on the type of flooring you select, you will have to work with different subs, which will affect the overall flooring process and timeline. We decided to carry the original wood floors from the rest of our main floor through to the kitchen instead of adding a tile or doing something completely different. I’m happy with that decision. The floors are beautiful and the subcontractor that our contractor used did a wonderful job. Even my uncle who is very knowledgeable about wood and flooring (as he used to be master carpenter) commented on the flooring looking good. It matches really well with the old floors, which makes me super happy. To make the floors match we did have to request to have them be the top nail installation and I was extremely specific about using the same wood (white oak vs the red they wanted to use) and the exact same stain we had used on our other floors when they were refinished. As I mentioned above about specifics, the exact flooring specs were not included in the initial budget in our contract. The contractor only included basic flooring prices, so our flooring materials and labor were… surprise, change order! Also, we did have to spend two nights in a hotel to avoid the harsh fumes of having the floors finished. So be prepared for that too!
If you use tile one thing to keep in mind is lead times. The lead time of tile often sets projects back and that’s an element that has NOTHING to do with your contractor. Be aware of leads times way ahead of the project for all the materials and finishes you select because that will directly affect the timeline of the project!
Most Important things to keep in mind with flooring:
Lead Times
Budget
Subcontractors
Our French Range
Appliances
Appliances like tile can majorly affect your timeline in a renovation. Not only do you need to consider quality and budget with appliances but also lead times are super important. When we were selecting the range I was back and forth between the Lacanche ranges and the La Cornue ranges. In the end the La Cornue was a little more affordable and the lead time was 2 to 3 months less than a Lacanche range. All of our other appliances were readily available except for the sink, which was handmade to order and took double the projected lead time. Thankfully our cabinets had major setbacks as well so the sink was not the only reason for holding up our timeline.
Things to think about with Appliances:
Lead times
Budget
Customer Service i.e. delivery and repair services - we chose to order through Albert Lee because they have some of the best customer service and repair services in Seattle area.
Our kitchen in progress
Cabinets
Okay, the cabinets have been our most major issue in this entire project. I would partially credit that to not having the budget for completely custom cabinets with this project. Hands down custom would have been a better direction - however that very easily could have come with a huge amount of unforeseen obstacles too. We worked with a designer/distributor who came recommended. She has been a pleasure to work with and very accomodating. Even though there have been a few minor mistakes with her cabinet order (that is not uncommon), the majority of the issues have come about through the manufacturer.
The company that we are having manufacture our cabinets has seemed to become completely confused and made so many mistakes on our order. I think partially due to our designer being so accommodating in helping us create cabinets and layouts that are pushing the boundaries of their semi-custom capabilities, the manufacturer has not been able to keep up with our non-standard order. This although is not entirely acceptable (in my opinion), can be quite typical where manufacturers make mistakes on atypical orders. In the case of our kitchen we’ve had cabinet bases made to the wrong specs, bench seat bases made to the wrong specs, doors delivered with the wrong hinges and again replaced without hinges. Which has all set us back at least 8 - 12 weeks beyond the initial lead time…
If you have the budget for custom cabinets make sure you keep in mind the lead times will be up to 12 - 16 weeks out. For standard not custom cabinets (also almost always made to order) you’re looking at 6 - 8 weeks for lead time. Also, if you’re customizing paint colors, be sure to add at least two weeks on to your lead time to make sure you get the paint samples right.
So to recap:
Things to think about when selecting cabinets:
Custom vs. semi or non custom - this decision is typically initially made in terms of budget, design needs, then lead times.
Lead Times
Fridge handles by Water Street Brass
Hardware
Hardware pretty much always has a lead time and for this project it was about 6 - 8 weeks for each item, from the sink faucet to the handles. Especially since I selected unlacquered brass for the hardware. Even though it’s becoming more popular, unlacquered brass seems to be one finish that is not typically stocked. So keep in mind lead times when selecting hardware.
Super White Dolomite paired with French Gray
Countertops
We selected our countertops very early on in the process because I wanted to see how my paint color selection worked with the counters. When selecting natural stone you have to keep in mind the availability of the slabs you choose. If you select a countertop that does not have a large amount of stock than you may have issues later on if the counters are cut wrong. We have had mostly positive results here, however our fabricator did completely forget to do include the drainer grooves. They will have to be coming back and cutting those on site, which does create a certain level of anxiety for me to honest…
Backsplashes
Our Splashbacks (as the Brits and Aussies like to call them) are going to be fabricated in the same material as our countertops so luckily we don’t have to work with an entirely new contractor on those. If we were doing tiled splashbacks we would have to consider lead times and potential issues that can arise there. I have heard many times from other designers and friends about tiling nightmares or mistakes made. I’ve even had some unexpected tile implementation on my own projects that weren’t worth the extra time or material to be redone. Tile is a tough component and you should have realistic expectations that this is one area that can go wrong quite frequently. On the other hand a good tile contractor is like a gift from the gods!
Lighting
Last but not least on my list, is lighting. I ordered all of my lights very early on for this project. But with other projects we have had to deal with lead times being pushed back just from the lighting. Light fixtures (especially luxury lighting) is made to order and can take a very long time to fabricate. Another major factor in lighting is finishes not being entirely controllable and breakage. Be aware to open light fixtures as soon as they arrive in the mail and inspect them very carefully. The sooner you find an issue with the light fixtures the more likely you are going to be able to resolve it.
Important lighting issues that can come up:
Breakage - open every box as it arrives
Placement of electrical - wiring and actual fixture placement. We have to move our sconce up because I made a mistake in placement. And my electrician made a mistake on the wiring in terms of which switch should be set where…. even with a detailed lighting plan.
If you haven’t completely scanned this post and read all the way to here, I applaud you. I hope this has been helpful and that I haven’t managed to miss any major details. If so, please feel free to comment, if it’s a major element I would be happy to edit the post and add that in. Also, I would be more than happy to hear about any renovating nightmares or lessons learned, so please speak up! We could all benefit from hearing about others’ experiences.
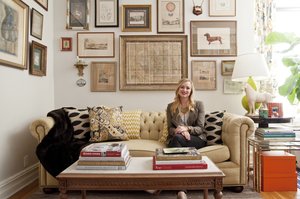